Common quality problems and solutions of cement well tubing equipment
Hello everyone, this issue's editor brings you new content. Reinforced concrete well pipes are formed using centrifugal technology, steam cured, and water cured. Abnormalities in the mix ratio of raw materials, centrifugal operation process, maintenance system, and other aspects, as well as cement well pipe equipment, may lead to the generation of cracks.
Hello everyone, this issue's editor brings you new content. Reinforced concrete well pipes are formed using centrifugal technology, steam cured, and water cured. Abnormalities in the mix ratio of raw materials, centrifugal operation process, maintenance system, and other aspects, as well as cement well pipe equipment, may lead to the generation of cracks. In the mixture ratio, the water cement ratio is too high, resulting in a larger remaining water cement ratio after forming. During steam curing, due to high temperature, some water evaporates, causing surface shrinkage and causing cracks on the inner wall of the well pipe.
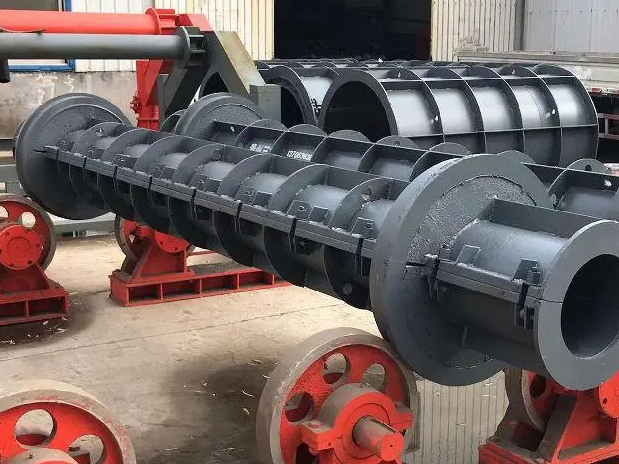
The well tube formed by centrifugation has poor control over the steam delivery system during steam curing. If the heating rate is too fast, on the one hand, the water at the pipe wall evaporates too quickly, resulting in a large humidity gradient; On the other hand, there is a large temperature difference inside the pipe wall, and water films and pores are easily formed at the interface between the aggregate and cement mortar, which form a concentration of temperature gradient and temperature gradient stress. Therefore, it is easy to control the generation and development of cracks. In severe cases, there may even be bubbling on the inner wall of the wellbore, with a depth of 3-8mm, which seriously affects the appearance quality of the wellbore and even makes it unusable. After the centrifugal molding is completed and lifted into the pool for steam curing, cracks are caused by the collision of the cement well pipe mold due to factors such as operators and machinery. After the steam curing demolding, the well tube is lifted into the steam curing pool before it cools down, and the sharp temperature difference will cause shrinkage cracks on the pipe wall. The demolding strength is too low, which leads to the occurrence of cracks due to external forces during demolding. The main reasons for stone exposure and roughness on the inner wall include factors such as raw material ratio, well pipe mold, and process operation.
When the sand content in the raw materials is low or the water cement ratio is small, the resistance between the mixtures increases during centrifugal molding. When the centrifugal force is less than or equal to its comprehensive resistance, it is difficult for the coarse aggregate and cement mortar to layer, the mixture is also difficult to compact, and the inner surface cannot form a rich cement slurry layer, resulting in exposed stones and uneven roughness defects on the inner wall. When the water cement ratio is too high, due to the easy formation of a water film between the coarse aggregate and cement mortar, the cement slurry and water are discharged together during centrifugation, resulting in a lack of cement slurry on the inner surface and a rough and uneven phenomenon. The editor will share the content of this issue here first. If you have any questions or want to learn more information, please leave a message to the editor!